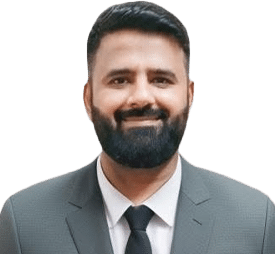
Senior Functional Consultant
Subscribe to the newsletter
When it comes to inventory management and optimization in a retail business, every box, every product, and every shipment counts. In this article, we explore the power-packed inventory carton management solution, redefining how businesses optimize their supply chains.
What is carton management for inventory?
Carton management involves systematically handling and tracking containers within the supply chain, particularly useful for intercompany sales or bulk shipments. It minimizes packing errors, reduces scanning costs, and streamlines the shipment and receiving process. At Confiz, our customized approach towards carton management enhances automation in Dynamics 365 Finance and Operations, combining standard excellence with tailored automation for efficient and adaptable retail operations!
Let’s break down carton management for inventory into three key points:
- It is a functionality that allows businesses to optimize the packaging of items for shipment into cartons/containers or boxes.
- At the time of receiving, the user scans the carton barcode, and all the packed items will be marked as received in Dynamics 365.
- Can be used for intercompany sales and transfer orders for retail stores.
Pre-requisites for getting started
To benefit from carton management, you must have Advance Warehouse Management System in D365 enabled. Below are the brief details of AWMS setup:
- Storage dimension – Should be enabled for site, warehouse, location and enable the use warehouse management process.
- Reservation hierarchy – Should be enabled on location level.
Unit sequence groups should be joined. - Warehouses with AWMS should be enabled with location profiles and locations created.
- Packing profiles, containers, warehouse workers, mobile device menus should be created.
Note: Retail stores warehouses don’t need to be enabled to AWMS.
Functionality overview
Let’s review the functionality for both scenarios i.e. intercompany sales and transfer orders:
Carton management for intercompany sales
Carton receiving process against purchase order
When the sales order is processed it is time to receive the stock against the purchase order. On the warehouse dock, assume a number of cartons have arrived. Each carton contains inventory i.e. jewellery items, cosmetics, stitched clothes, shoes and bags etc. If a user verifies and marks each item as registered of product receipt in the system, this will consume a lot of time.
With carton management enabled in Dynamics 365, the user will just have to login to the warehouse mobile device and scan the carton barcoded. All the packed items will be registered in relevant purchase order. The process is explained via the figure below:
Solution walkthrough in Dynamics 365 Finance and Operations with AWMS
Let’s review the functionality step by step. In the below screenshot, we can see that the work against sales order has been completed and stock is placed on the packing location:
Now, the warehouse worker will pack the stock into a container by scanning the item bar codes. This will generate container ID:
Once all the items are packed into the container, the user will close the container and confirm the shipment. See the below screenshot of closed container.
Note: Shipment can be auto confirmed in batch process after container close.
Attach the container bar code
You are now ready to print the carton barcode and paste it on the carton physically:
Receive the container
The Inventory will arrive to the receiving company’s warehouse against intercompany purchase order. Now without opening the carton, the warehouse worker will login to warehouse mobile device and scan the cartons to make registration of the packed inventory.
Below is the screenshot of the mobile device, displaying the container number:
After clicking OK, it will feed the information i.e. the purchase order number and all the packed items information with quantity that is packed in scanned carton:
After confirmation, go to the purchase order and verify that the stock is registered on floor (main) location:
Inventory registration
Now the user will generate and post product receipt against registered inventory in the purchase order.
Carton management for transfer orders
Transfer order process
Once the transfer order inventory arrives at destination retail outlet, the user will log into Dynamics 365. In a custom form, the user will select from and destination warehouse and without opening the carton, he will scan the carton bar code.
After scanning, it will show the lines of inventory that is packed in the cartons.
Note: As mentioned in the start, the retail outlet user doesn’t need to use warehouse mobile device because retail warehouses are not enabled for AWMS.
Solution walkthrough in D365 Finance and Operations
Let’s review the system’s screens. Assuming that the transfer order work has been completed, and stock is placed on packing location for containerization.
Now the container is closed, and shipment is confirmed:
Carton scanning at time of transfer order receiving
Select the from and destination warehouses, and scan carton barcodes without opening the carton. It will show the packed items’ detail. Verify the details and click on save. An auto batch job will mark the transfer order as received in Dynamics 365:
Technical aspects to remember
Above functionality of carton management is available D365 F&O as standard feature. There is a standard data entity which is “Inbound ASN V3” and it contains 5 child entities that run in sequence. An XML file must be imported in Inbound ASN V3 which will be creating a packing structure in the intercompany purchase order load lines.
As per standard process of Microsoft, you need to import the XML file into Inbound ASN V3 and run it.
We have worked with developer for automation of Inbound ASN and set the data batch job on recurring.
Below is the content of the XML file:
<?xml version=”1.0″ encoding=”utf-8″?>
<Document>
<WHSInboundLoadHeaderEntity TractorNumber=””>
<WHSInboundShipmentHeaderEntity VENDORSHIPMENTID=”” VENDORADDRESSCOUNTRYREGIONID=”” VENDORADDRESSSTREET=”” VENDORADDRESSSTATEID=”” VENDORADDRESSCITY=”” VENDORADDRESSZIPCODE=””>
<WHSInboundLoadPackingStructureEntity LICENSEPLATENUMBER=””>
<WHSInboundLoadPackingStructureLineV3Entity PACKINGSTRUCTURELICENSEPLATENUMBER=”” PURCHASEORDERNUMBER=”” ITEMNUMBER=”” PRODUCTCOLORID=”” PRODUCTSTYLEID=”” PRODUCTSIZEID=”” PURCHASEORDERLINENUMBER=”” QUANTITY=”” UNITSYMBOL=”” />
</WHSInboundLoadPackingStructureEntity>
</WHSInboundShipmentHeaderEntity>
</WHSInboundLoadHeaderEntity>
</Document>
Summing up
We hope this guide provides valuable insights into carton management for your inventory. If you need assistance or encounter any issues, feel free to contact us at marketing@confiz.com, we’re here to help!